What better way to learn what makes a guitar really sing than by first resurrecting hundreds of choked starlets? Enter: Butch Boswell, veteran of over 20 years’ experience in the repair world whose own guitars belt it out with clarity and gusto. We recently got to check out a guitar Butch had custom built for a client, and that got our attention in a big way. When Butch approached us to sell another custom build, this time a 0.5 12-fret in Brazilian Rosewood and Italian Spruce, the answer was a resounding yes. Butch was happy to sit down with us to talk about life and lutherie and snap a few photos of his (impressively clean) shop and wood collection. Check out that conversation below, and stay tuned while we finish the listing for the Boswell 0.5!
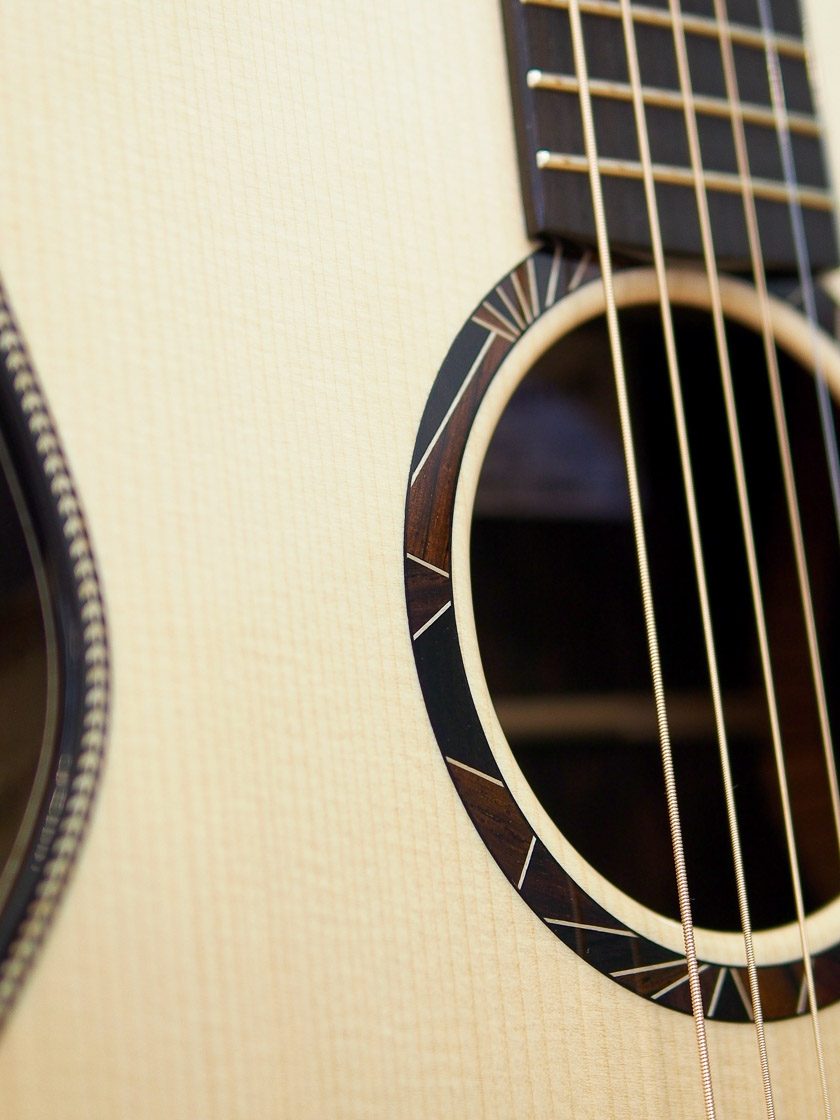
LW: Before building guitars, you enjoyed a successful career in repair work. Can you speak to the ways in which your building has informed your subsequent repair work, and vice versa?
BB: I think that repairing instruments all these years influenced my current work more than the other way around. Throughout my career in guitar repair, I performed every step involved in guitar building hundreds of times. When it was finally time to build a guitar, it was just a matter of stringing each step together in the proper sequence. Having said that, building, especially at this level, has still proven to be a huge challenge. But, learning the fundamentals through years of repair work truly helped to lay a very solid foundation.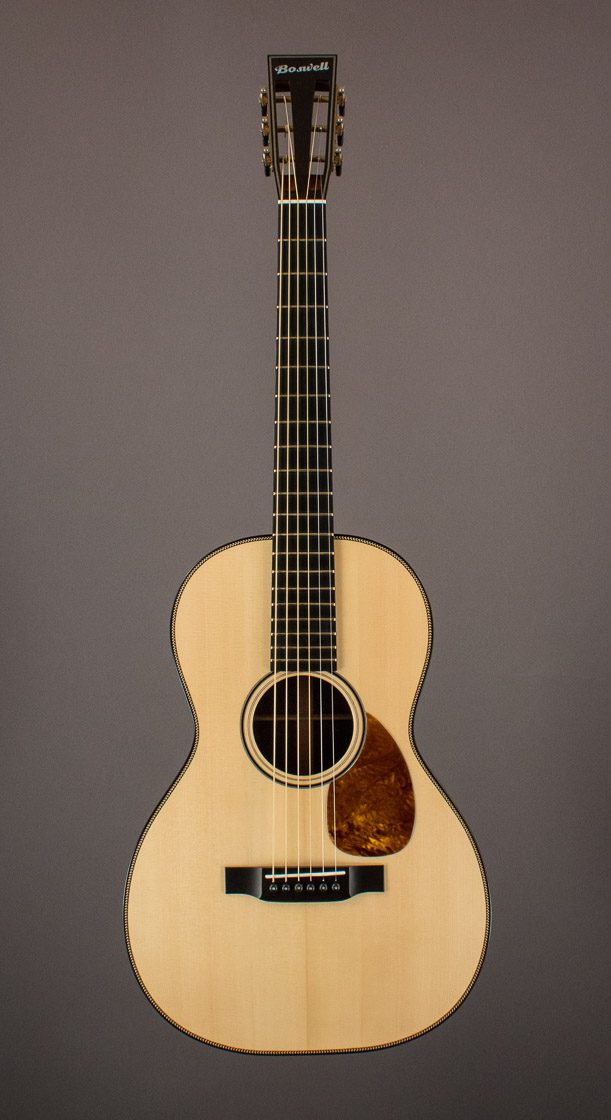
LW: Talk to me about your current shop arrangement. How do you manage workflow?
BB: I absolutely love the space I’m currently in. It’s well lit, small, easy to keep clean, and probably most importantly, very efficient in how it’s laid out. I can build for a few hours, then if I have to, I can easily segue into some accumulating repair work. As far as how well I manage my workflow, well, that’s something I’m still trying to figure out! For one person to manage what is essentially two completely different careers, both of which could keep me pretty busy, has always proven to be the challenge. (see photos)
LW: Who are some of your favorite guitar players? Have you built instruments for any of them?
BB: I don’t really have a favorite player, but I could take up this entire blog with players I admire and listen to! I listen to music in my shop all day, every day. I have several players in my accolades section that are absolutely the top of the top. Tim Pierce, Steve Trovato, Danny Pelfrey, Danny Weis, Tim Bluhm. These are all guys that have played with every big name out there, and their catalogue of work is seriously deep. They may not be immediately recognizable household names, but these are some of the guys behind the names we all know. They are all fantastic players and performers, and I’m so proud to have each one of them playing my instruments.
LW: Many builders have a particular guitar that has heavily influenced their body of work. Do you have an archetype of your own?
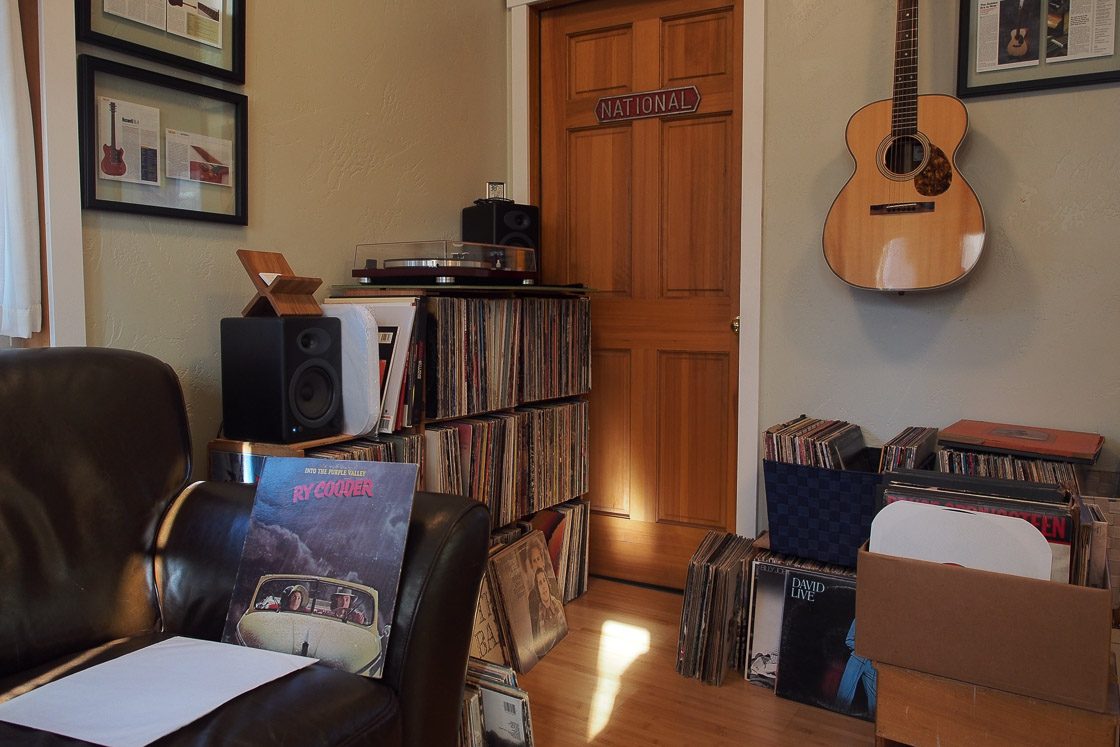
BB: For me, having come up in the repair and sales world, I have had my hands on more vintage Martin guitars than probably anything else, but I have also worked closely with Santa Cruz Guitars, Collings, Taylor, etc. My repair work has been a study in the evolution of the flattop steel string acoustic guitar. So, when I built my first guitar, you can imagine what it looked like! It’s a dead ringer for a 000-28. Do these makers still influence my work today? Probably not. I have stepped out into my own look and sound over the past few years, including my own aesthetic and combinations of materials, my own take on bracing and strength of materials, and my own sound.
LW: Please describe your approach to voicing an instrument. How did you first find your voice, and how do you continue to experiment?
BB: Like I said before, when I first got started with building, I was a repair guy, and really just copying what I had seen for years, both inside and out. But as I began to find truly inspiring materials, which wasn’t easy, and as I started to experiment with my own bracing ideas, my instruments started to sound more and more my own. I have tried various forms of voicing techniques, but the one thing that I always seem to come back to, the one thing that seems to never let me down, is my ear. I have worked in guitar shops and played music professionally for upwards of 25 years now. I always say that tone is the last thing for a player to learn. Developing one’s ear is not an easy thing to do. But,
when you are subjected to it day in and day out for more than half of your life, inevitably it becomes somewhat engrained. When I first started building, I already knew what I was hearing when I would tap on a soundboard even before I could describe what was going on. Nine times out of ten, when I look inside of a production guitar, I see a very over-built instrument. They’re having to do that to protect themselves against warranty claims, but they’re also killing the tone of the instrument. Many things have led me to where I am today with the voice of my instruments (playing music, repairing, my education in engineering), but the one thing I know I can truly count on every time is my ear.
LW: We recently received your 0.5 #0026—woah. What were your goals in building a guitar halfway between a 0 and a 00?
BB: Well, this wonderful little box was a custom order for a customer. He wanted the vintage Martin style framework, but with a little more umph under the hood! So, I had this incredibly special set of Brazilian that was just a touch small for a traditional 00 size guitar. So, we reduced it slightly to make the set work, but still managed to keep it a bit larger than an 0 size. Coincidentally, I got several very old Italian spruce tops from a retired builder. They were much too small for most current popular models. The two were perfect for one another, and No. 0026 was born!
LW: What do you enjoy doing outside of building and repairing instruments?
BB: I’m a dad and husband before everything else. So, when I’m not getting my ass kicked in the shop, I’m usually getting it kicked at home. I have three little ones, ages 8, 6, and 2, and they love to play with Dad. I’ll come home, ice my shoulder, then go jump on our huge trampoline for an hour or so, come back in and ice something else. I love playing with my kids, and I love being a dad. Outside of that, Bend, OR is an amazing place to be if you like being outdoors. I do a lot of mountain biking, and have vowed this summer to take my family camping several times.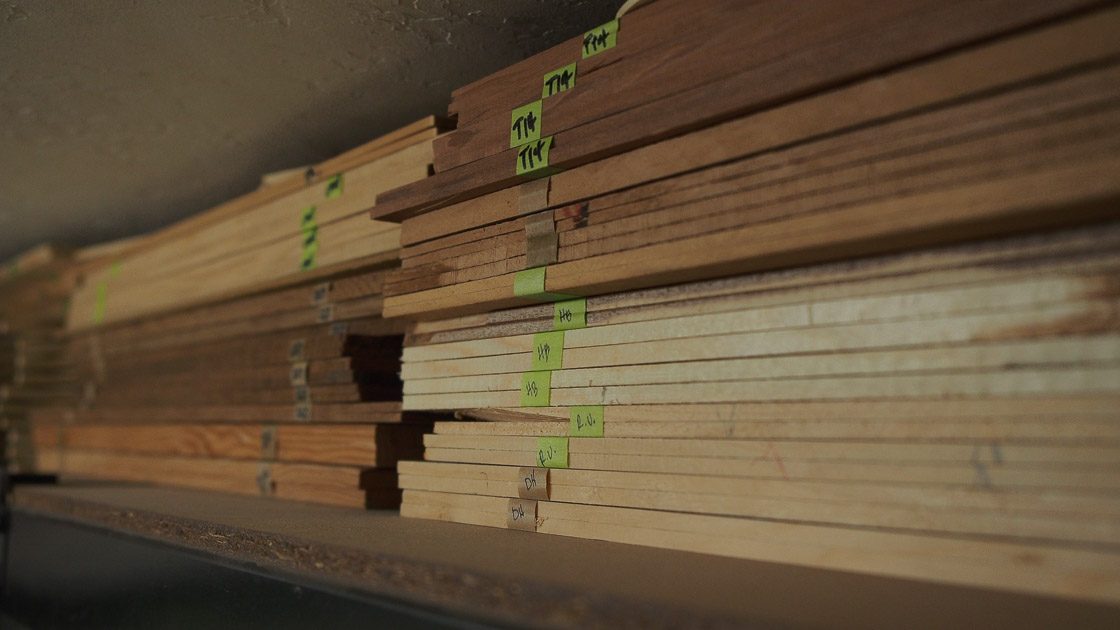
LW: What music are you listening to right now?
BB: At this exact moment, it’s Ry Cooder, Into the Purple Valley, and Jackson Browne, Saturate Before Using. I have a record collection that is a touch out of control, so it can be VERY different on any given day! (see photos)
LW: Your current models appear to be firmly rooted in the traditional style. In your eyes, what sets your guitars apart from the pack?
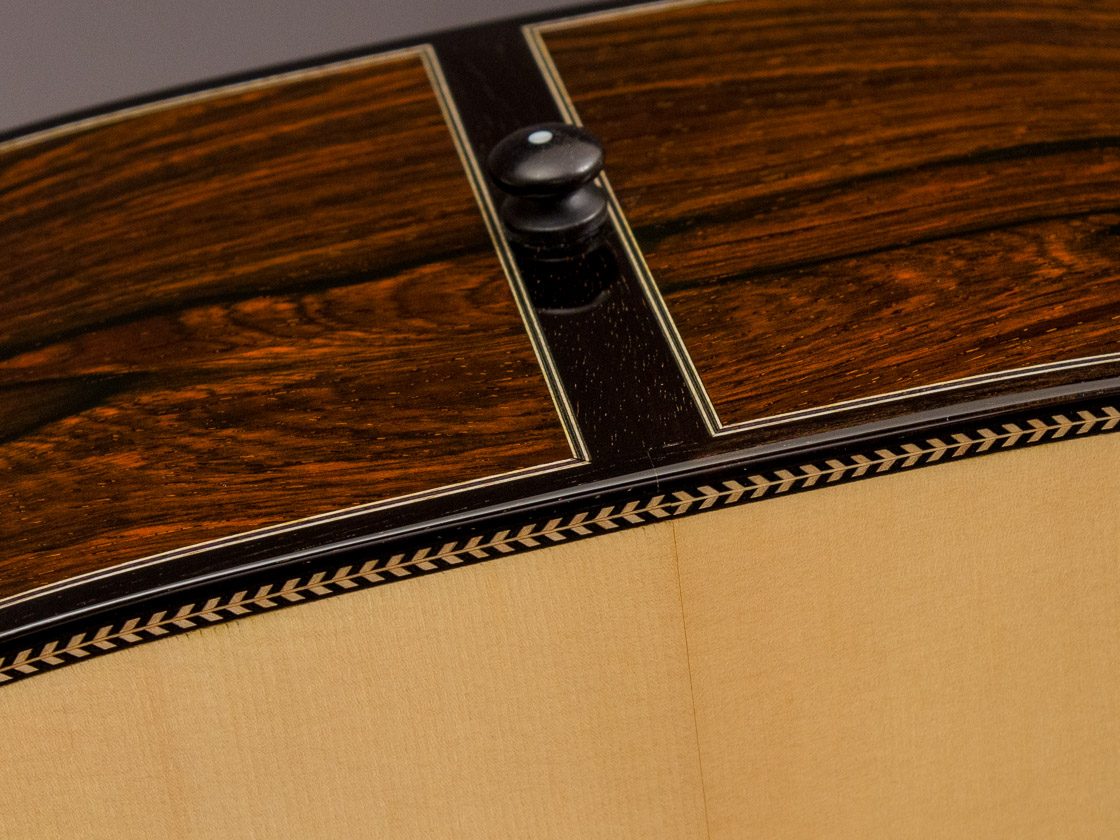
BB: Most of my body shapes are very traditional sizes, but they have been changed slightly to suit my goals. More and more though, I’m excited to be able to experiment with more and more interesting wood combinations and aesthetic. Rosette work is one of my favorites, and my “Tiled Mosaic” look is getting more and more popular (see photos). I strive to keep a high level of consistency in color, grain, and materials throughout a build, and I think I am somewhat blessed with an eye for putting together interesting and complimentary designs. One of the biggest things that separates me from the pack though, would be my experience in a very high level of repair work I’ve been involved with for 20+ years. Making a great-sounding box is one thing. Putting it together with the neck correctly, setting the neck angle, fretting it, and making it play masterfully is another set of skills altogether.
LW: If you had not become a guitar maker, where do you think life would have led you?
BB: Politics. Ha! No way. I see every day how lucky I am to have three healthy children. They play hard, they’re smart, and they have a leg up in this world because they have parents and family that care about them so deeply. A lot of kids don’t have that. I think about that sometimes, and I wish I could be more involved as a Big Brother, or involved somehow in helping kids that are just less fortunate than my own. If I wasn’t building guitars, I truly have no idea what I would be doing. It’s a terribly hard path we luthiers have chosen, and there are days I have felt like giving up, but it’s what drives me. To say I’m passionate about my work is a gross understatement. I love it, and I’m so fortunate to have what I have, and be where I am in my career at this very moment.
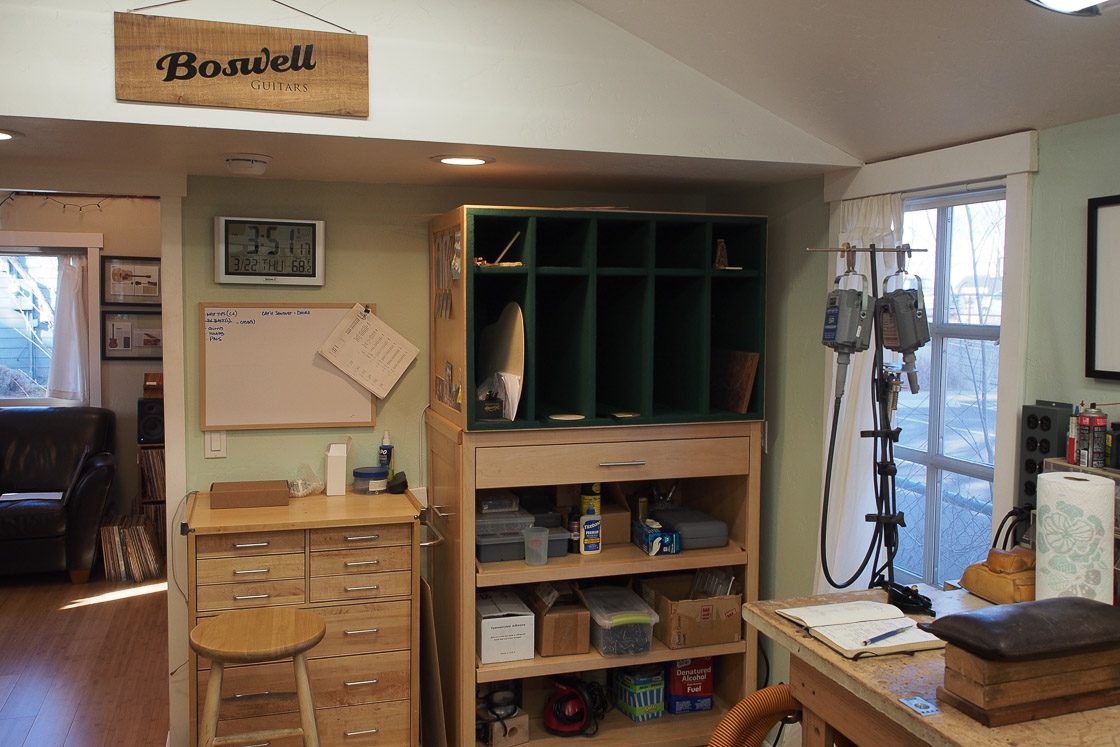